Cite report
IEA (2019), Multiple Benefits of Energy Efficiency, IEA, Paris /reports/multiple-benefits-of-energy-efficiency, Licence: CC BY 4.0
Productivity
Efficiency leads to productivity gains in particular by lowering maintenance costs and increasing production yields per unit of input. In addition, improvements in operation and process reliability, which can result from efficiency gains, lead to reductions in equipment downtime, shutdowns or system failures. Optimising processes to enhance efficiency can also reduce staff time required to enhance operations and scheduling while reducing the risk of human errors.
More benefits are possible in an Efficient World
Between 2000 and 2017, energy intensity – final energy consumption per unit of gross value added (GVA) – in the industrial sector decreased by 25%. Greater productivity gains are still possible from the adoption of cost-effective energy efficiency measures, as described by the IEA Efficient World Scenario (EWS). By 2040, manufacturing industries could produce nearly twice as much gross value-added from each unit of energy use.
Energy management systems enable productivity benefits for industry
An energy management system creates the structure and processes for a company to monitor energy consumption and improve efficiency. In addition to energy savings, the adoption of an energy management system can lead to industrial productivity gains by improving energy performance and overall system efficiency. Other benefits can include enhanced production and capacity utilisation, reduced resource use and pollution, and lower operation and maintenance costs – all of which result in increased value generation, and thus improved competitiveness.
Results from companies participating in the United States Superior Energy Performance (SEP) Program provide an indication of the energy efficiency and productivity benefits obtained from the implementation of an energy management system. SEP is a voluntary program in which companies implement ISO 50001 (the global energy management system standard) and energy-saving projects, in order to show that efficiency has improved in accordance with established targets.
In 2015, the energy performance improvement of certified Schneider Electric sites was over 60% greater than non-certified sites. This additional improvement is also demonstrated through quarterly energy savings achieved by SEP certified companies. Quarterly energy savings prior to certification averaged 3.2% and increased to 7.5% in the four quarters after certification and 14.2% in quarters five to seven. In all cases, the improvements observed for certified sites increased over time, illustrating that the benefits of energy management can grow as sites became more knowledgeable and experienced.
Energy performance improvement of ISO 50001 and SEP certified Schneider Electric sites compared to non-certified sites, 2012-15 (left) and verified average quarterly energy savings from SEP certified companies, pre- and post-certification (right)1
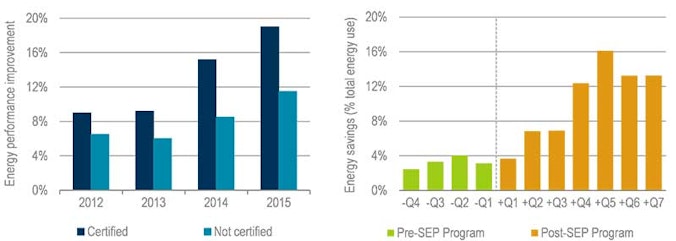
Note: Based on data analysis conducted by Schneider Electric
The United Nations Industrial Development Organisation (UNIDO) works with companies in developing economies to implement energy management systems in line with ISO 50001. Data from nine of these companies reveals that on top of savings resulting from the implementation of efficiency projects, they achieved additional “energy management system unique” savings, linked to improvements in staff awareness of energy efficiency; energy management capability; daily routine operations; and staff accountability. Following the implementation of an energy management system in these nine companies, projects were implemented that led to electricity savings of over 26 GWh. However, there were also an additional 8 GWh of “energy management system unique” savings, which accounted for between 1% and 19% of total electricity use in the companies analysed and 12% to 80% of the total savings.
Comparison of project and energy management enabled savings2
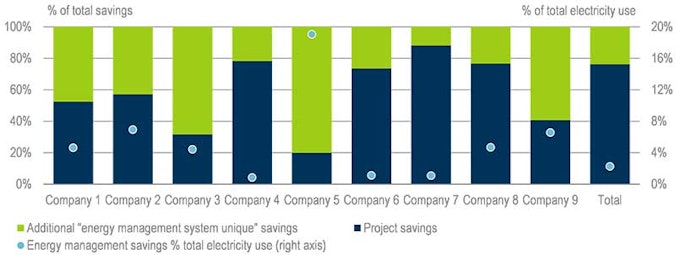
Quantifying multiple benefits
While translating non-energy benefits into strategic and financial outcomes may be challenging, some companies have been able to do so successfully.
A Swiss surface treatment company, for example, was able to improve dramatically the business case for an energy efficiency project by factoring in non-energy benefits. When project planners considered only energy savings of a project to optimise the performance of rectifiers, they calculated a simple payback of 6 years. However, when the planners considered financial outcomes derived from non-energy benefits – such as lower maintenance costs, reduced cooling water use and other operational improvements – the simple payback plummeted to less than 1 year.3
References
IEA (2018), Energy management systems and digital technologies for industrial energy efficiency and productivity
UNIDO (personal communication 21 June 2018)
Cooremans C., Eco’Diagnostic, Monney L., Greenwatt, Canton of Vaud Energy audit program, Presentation of 31 May 2016. www.vd.ch/fileadmin/user_upload/themes/environnement/energie/fichiers_pdf/EE_centre_de_profit_201606.pdf.
Reference 1
IEA (2018), Energy management systems and digital technologies for industrial energy efficiency and productivity
Reference 2
UNIDO (personal communication 21 June 2018)
Reference 3
Cooremans C., Eco’Diagnostic, Monney L., Greenwatt, Canton of Vaud Energy audit program, Presentation of 31 May 2016. www.vd.ch/fileadmin/user_upload/themes/environnement/energie/fichiers_pdf/EE_centre_de_profit_201606.pdf.